Sustainability
Our approach to sustainability
Our approach to sustainability
KeyPlants’ position as a leader in off-site modular manufacturing has a clear link to sustainability. Our ambition is to deliver innovative life science facilities and projects that contribute to a healthier world while maximizing the positive sustainability impacts of our modular manufacturing process. For KeyPlants, sustainability also means incorporating sustainability principles into our design process and value chain, conducting business in an ethical way and in alignment with our company values, and fostering safe, respectful, and inclusive work environments.

Sustainability strategy
Sustainability strategy
KeyPlants’ strategy and sustainability work demonstrate the ways in which KeyPlants can directly and indirectly promote sustainable development. KeyPlants’ Sustainability Strategy 2023-2025 centers on three strategic ambitions, which are coupled to six specific focus areas and to relevant UN Sustainable Development Goals (SDGs):
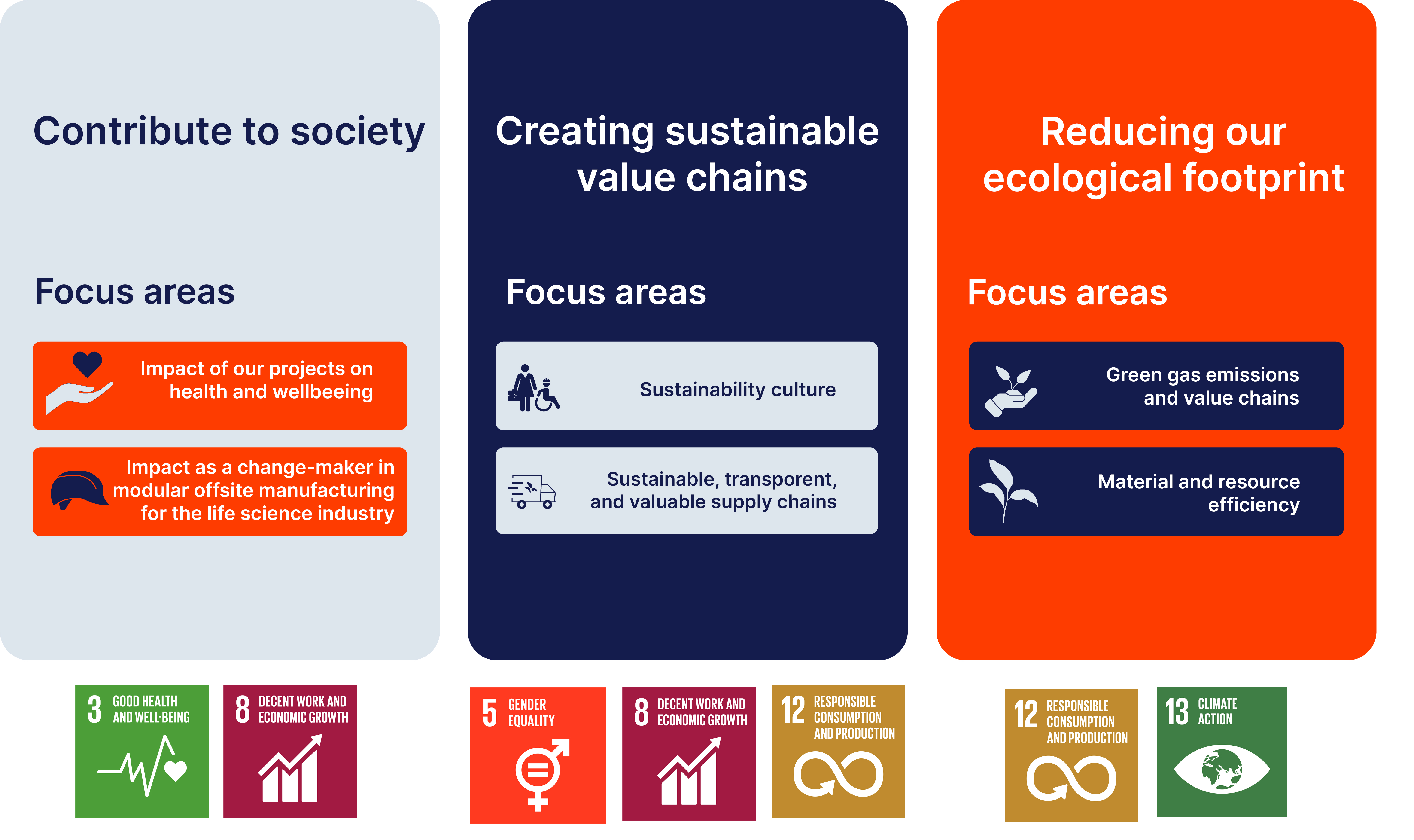
Sustainability report 2024
KeyPlants’ annual sustainability report contains more information about the sustainability efforts and performance of the KeyPlants companies related to the environment, health & safety, and social sustainability. It also describes our participation in external initiatives, such as SBTi, and the company’s work related to the UN Sustainable Development goals where we see the greatest potential for positive impact.
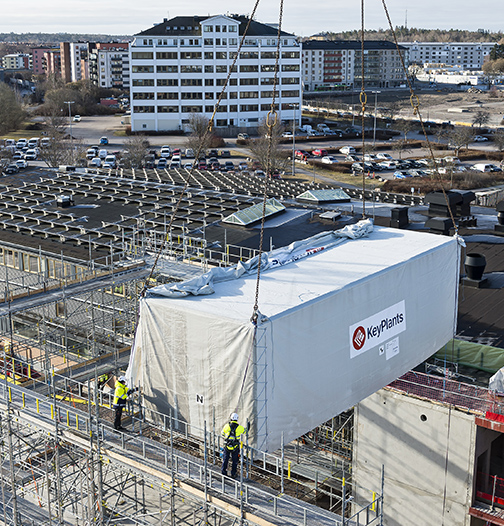
Our goals
Our goals
Make a substantial contribution to societal well-being
Integrate sustainability into all our value chains
Achieve close to net-zero emissions and employ a circular model
EcoVadis
Science Based Targets initiative
UN Global Compact
UN Sustainable Development Goals
KeyPlants has received two consecutive Gold ratings from EcoVadis, one of the largest providers of company sustainability ratings in the world. The Gold rating means that KeyPlants is ranked in the top 5% of companies assessed by EcoVadis.
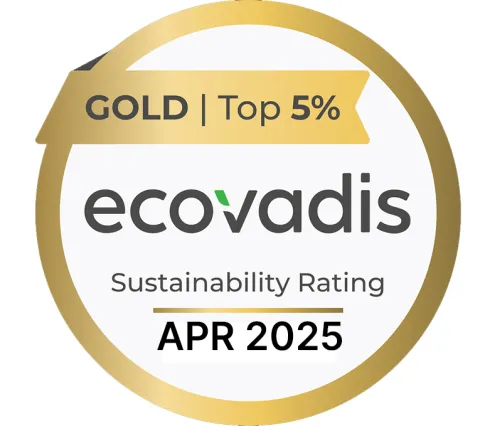
KeyPlants’ science-based targets for reducing greenhouse gas emission were validated in 2024 by the Science Based Targets initiative (SBTi), which mean that the targets are in line with the latest climate science research and efforts to limit global temperature increase to 1.5 °C.
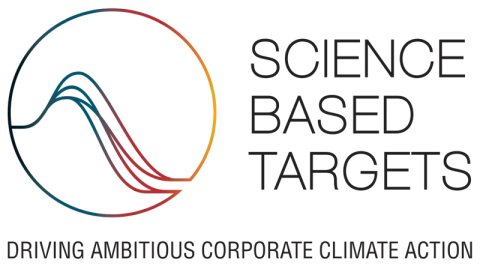
In February 2024, KeyPlants was accepted as a participant in the United Nations Global Compact (UNGC), the world’s largest corporate sustainability initiative. KeyPlants has committed to supporting the ten principles of the UNGC and to contribute to advancing the UN Sustainable Development Goals (SDGs).
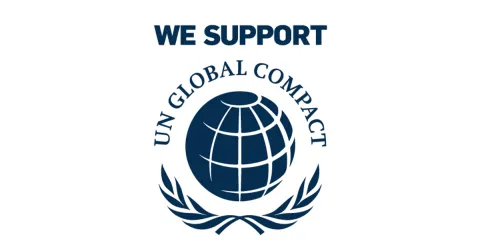
KeyPlants aims to contribute to the UN Sustainable Development Goals (SDGs), which are the United Nations’ blueprint for achieving a sustainable, peaceful, and prosperous future for people and the planet, through both the projects we deliver and the company’s own sustainability work. KeyPlants has identified five SDGs as being an integral part of our sustainability work.
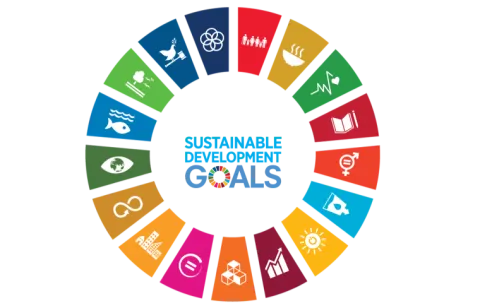
EcoVadis
KeyPlants has received two consecutive Gold ratings from EcoVadis, one of the largest providers of company sustainability ratings in the world. The Gold rating means that KeyPlants is ranked in the top 5% of companies assessed by EcoVadis.
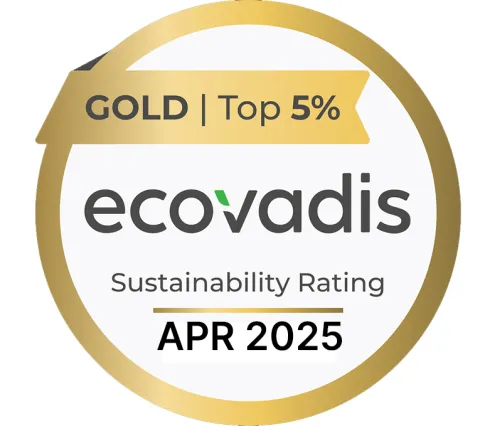
Science Based Targets initiative
KeyPlants’ science-based targets for reducing greenhouse gas emission were validated in 2024 by the Science Based Targets initiative (SBTi), which mean that the targets are in line with the latest climate science research and efforts to limit global temperature increase to 1.5 °C.
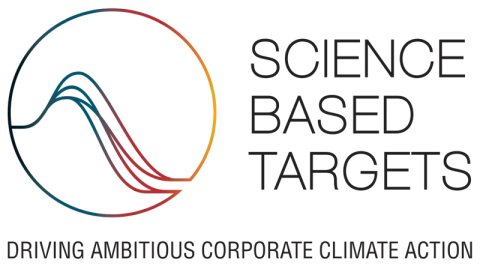
UN Global Compact
In February 2024, KeyPlants was accepted as a participant in the United Nations Global Compact (UNGC), the world’s largest corporate sustainability initiative. KeyPlants has committed to supporting the ten principles of the UNGC and to contribute to advancing the UN Sustainable Development Goals (SDGs).
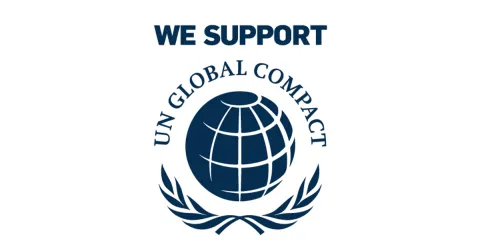
UN Sustainable Development Goals
KeyPlants aims to contribute to the UN Sustainable Development Goals (SDGs), which are the United Nations’ blueprint for achieving a sustainable, peaceful, and prosperous future for people and the planet, through both the projects we deliver and the company’s own sustainability work. KeyPlants has identified five SDGs as being an integral part of our sustainability work.
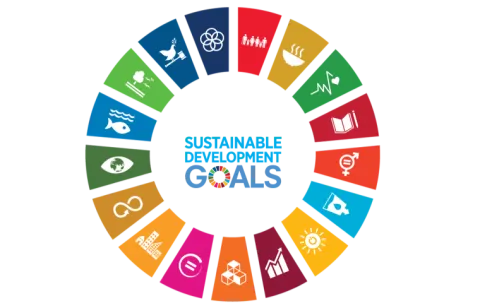
Contact
Contact
For questions about KeyPlants’ sustainability work, please contact Graham Kirn, Sustainability Controller, sustainability@keyplants.com
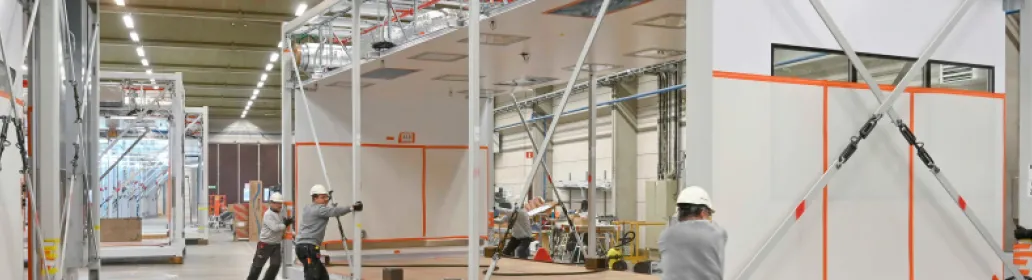