OFFSITE MODULAR CONSTRUCTION
Fabrication Services
Unmatched experience. Standard methods. Custom solutions.
Unmatched experience. Standard methods. Custom solutions.
When it comes to executing complex installations with precision, nothing beats experience. Our highly-trained workforce has decades of end-to-end project experience, specifically in designing, building, and installing modular facilities through offsite modular construction, all over the world. For over 45 years, we’ve developed standard, proven, quality-assured manufacturing methods, and our employees have gained valuable expertise from each and every project.
square meters indoors
square meters outdoor
ISO 9001, ISO 14001 and ISO 45001 certified manufacturing workshop in Emtunga
Save time and costs on site
Minimal disturbances on site
Shorter timeline
Greater sustainability
Strong, long-lasting facilities
Full control, less risk
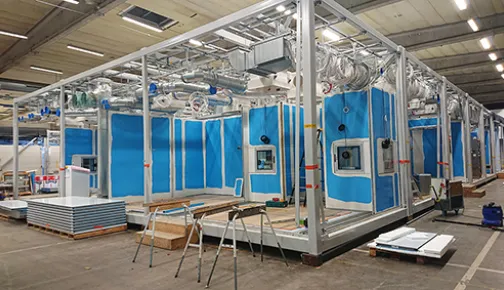
With installations made in the workshop, completed modular facilities are delivered, assembled, and commissioned by our team. This reduces risk and saves time and on-site costs.
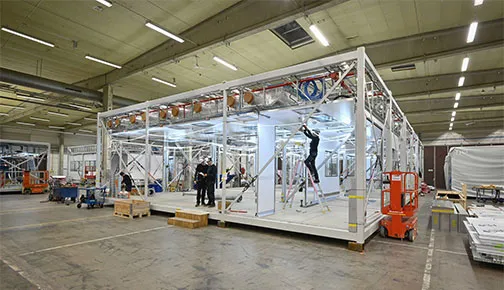
We aim to perform at least 85 percent of the work in the workshop, which means minimal disruption on site. This is a critical factor to consider, especially when the facility is surrounded by existing developments and your own day-to-day operations.
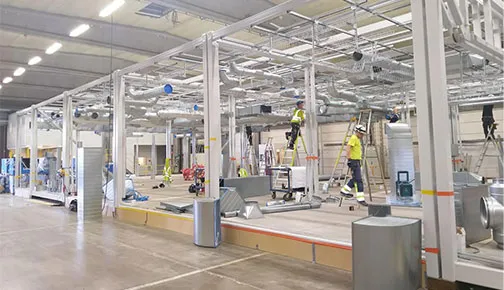
Since fabrication usually takes place in parallel with site preparation, your facility is completed faster. This means:
- Speedier access to new capacity and faster ROI.
- More time for potential and subsequent project stages.
During Fabrication
- Standardized, off-site manufacturing, with re-use of proven solutions, leading to lower energy utilization.
- Efficient manufacturing workflows and less transport, leading to lower energy utilisation.
- Prefabrication and installation in the workshop minimises transport and disruption on site, leading to a lower carbon footprint.
- Prequalification of materials, equipment and the entire modular facility through Factory Accaptance Test, leads to ease of commissioning and less travel to site.
During Operation
- Designing facilities with smaller footprint, with reduced HVAC and water consumption, leading to lower energy & utilities use.
- Minimal disturbances in existing operation results in reduced cleaning & product changeover time.
- Ease of modular expansion, adding footprint incrementally, reduces carbon footprint.
- Turnkey solutions which can be repurposed and relocated means there's less need for further construction projects.
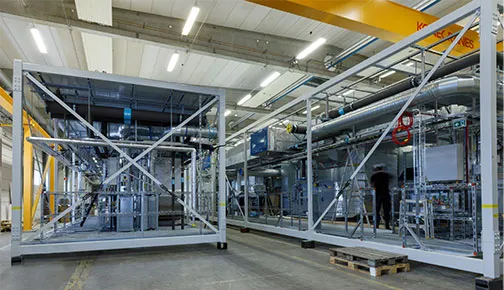
Our products are designed and built to last. Our robust, steel construction techniques make the modules stackable, and facilitate the installation of heavy process equipment for a high degree of prefabrication, and an effective work environment.
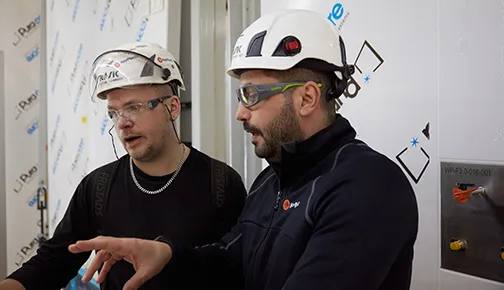
Offsite fabrication gives you complete oversight and control of your project. Our aim is for 85% of the fabrication to take place in our workshop, which results in a “plug & play” solution. This helps minimise risk as far as schedule and budget are concerned.
Save time and costs on site
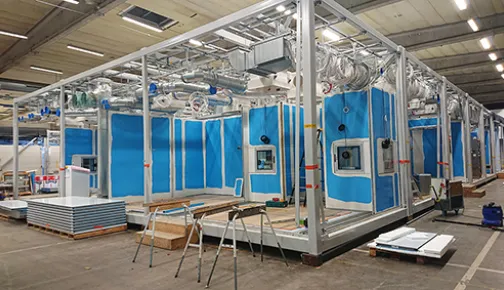
With installations made in the workshop, completed modular facilities are delivered, assembled, and commissioned by our team. This reduces risk and saves time and on-site costs.
Minimal disturbances on site
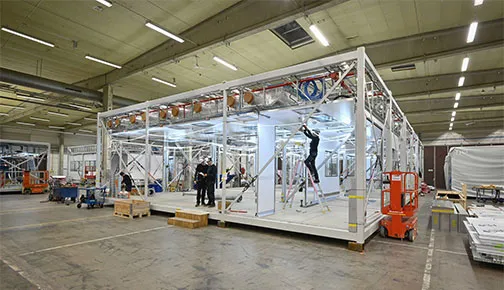
We aim to perform at least 85 percent of the work in the workshop, which means minimal disruption on site. This is a critical factor to consider, especially when the facility is surrounded by existing developments and your own day-to-day operations.
Shorter timeline
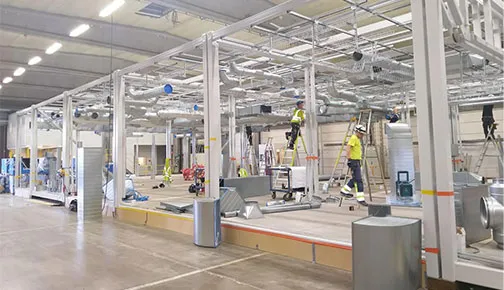
Since fabrication usually takes place in parallel with site preparation, your facility is completed faster. This means:
- Speedier access to new capacity and faster ROI.
- More time for potential and subsequent project stages.
Greater sustainability
During Fabrication
- Standardized, off-site manufacturing, with re-use of proven solutions, leading to lower energy utilization.
- Efficient manufacturing workflows and less transport, leading to lower energy utilisation.
- Prefabrication and installation in the workshop minimises transport and disruption on site, leading to a lower carbon footprint.
- Prequalification of materials, equipment and the entire modular facility through Factory Accaptance Test, leads to ease of commissioning and less travel to site.
During Operation
- Designing facilities with smaller footprint, with reduced HVAC and water consumption, leading to lower energy & utilities use.
- Minimal disturbances in existing operation results in reduced cleaning & product changeover time.
- Ease of modular expansion, adding footprint incrementally, reduces carbon footprint.
- Turnkey solutions which can be repurposed and relocated means there's less need for further construction projects.
Strong, long-lasting facilities
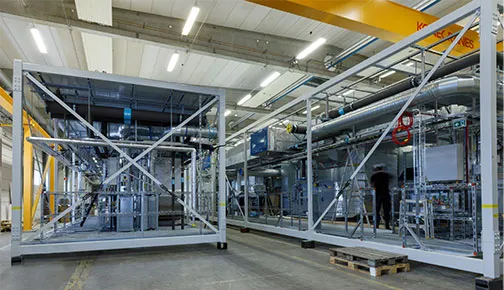
Our products are designed and built to last. Our robust, steel construction techniques make the modules stackable, and facilitate the installation of heavy process equipment for a high degree of prefabrication, and an effective work environment.
Full control, less risk
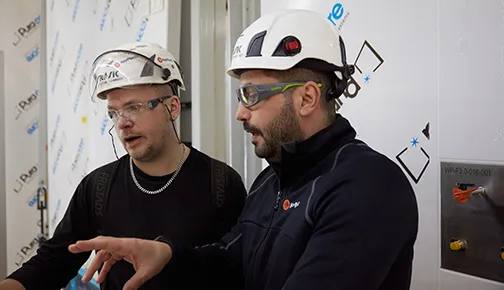
Offsite fabrication gives you complete oversight and control of your project. Our aim is for 85% of the fabrication to take place in our workshop, which results in a “plug & play” solution. This helps minimise risk as far as schedule and budget are concerned.
How we work
We deliver turnkey facilities, including process equipment, utilities and digital solutions, as well as facility upgrades and expansions. Our capabilities include full in-house design and modular fabrication, as well as subject matter expertise in biologics, aseptic filling, containment, and manufacturing of APIs and oral solids.
Fabrication off-site and indoors
After the KeyPlants team has completed the detailed design, fabrication drawings are produced and fabrication begins. Our modular facilities are made indoors under climate-controlled conditions. This prevents weather-related delays, and enables us to deliver clean, sealed modules to your site. It also improves safety.
Highest quality standards
Indoor fabrication, standardised methods, and ISO 9001 and 14001 certifications of the workshop are three of the ways we ensure quality. But quality and precision are delivered by human beings, not systems; and that’s where a workforce led by people with decades of experience matters.
Unparalleled on-site expertise
Every module is inspected and pre-tested, along with all its installed equipment, before we ship it to your site. This minimises the chance of any problems when the modular facility arrives on site. But any site can pose challenges, and it helps to have a team of experienced people on hand. Recently, one of our more experienced employees, someone who had installed our modules in over 30 countries, made a point of bringing along younger employees to his projects, so he could pass on as much knowledge and experience as possible before he retired.
Experienced, motivated employees
When employees are motivated and love what they do, they want to share their knowledge with their colleagues. They work well as a team, making sure everything is done correcty first time round on a project, which of course has an impact on your bottom line. Our ISO 9001 and 14001 certifications are important – and we are proud of them – but quality and precision are delivered by people, not systems.
HSE: More than policies
Take EHS, for example. At KeyPlants’ workshop, the way we work stems from mutual respect, from the cleaners all the way up management. And of course we have strict safety procedures in place. For example, anyone working more than 1.5 meters above the ground, has to be hooked up to safety lines. This is to reduce the risk of any injury, or lost time through injuries (LTIs). By working indoors, we also avoid outdoor risks, such as weather-related hazards. So, it’s not surprising that we have an excellent safety record, with almost no LTIs over the years; even though construction is one of the world’s most hazardous industries.
Innovative offsite modular construction for efficient project delivery
KeyPlants specializes in offsite modular construction, delivering pre-fabricated facility solutions designed for speed, precision, and compliance with industry regulations. Our modular facilities reduce project timelines and minimize on-site disruptions while providing the flexibility needed for future scalability.
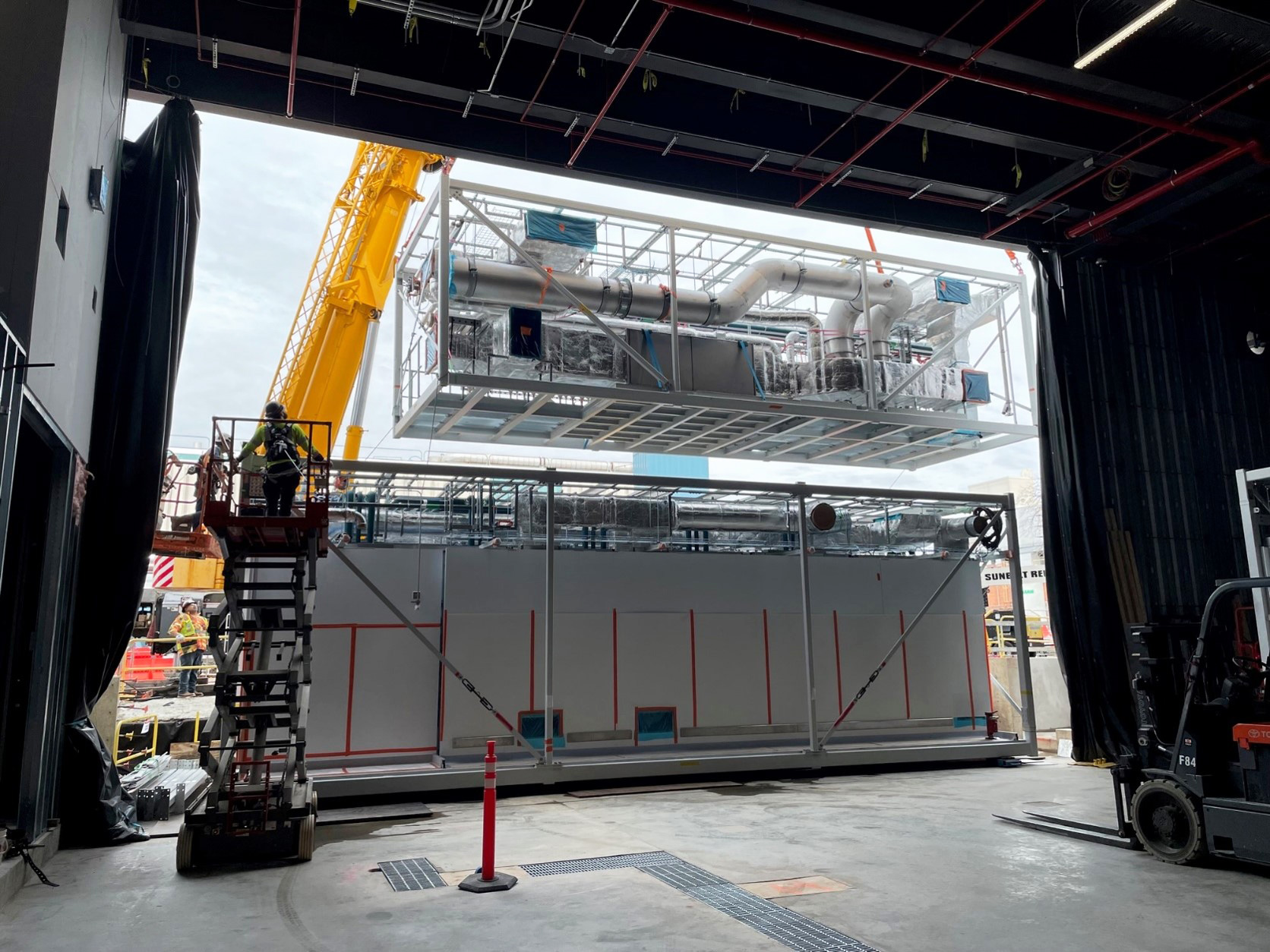
Offsite modular construction tailored to your needs
At KeyPlants, we combine advanced fabrication techniques with decades of expertise to deliver modular solutions that are ready for seamless installation. By completing up to 85% of construction in a controlled workshop environment, we ensure consistent quality, faster project timelines, and reduced on-site risks, making your facility operational sooner.
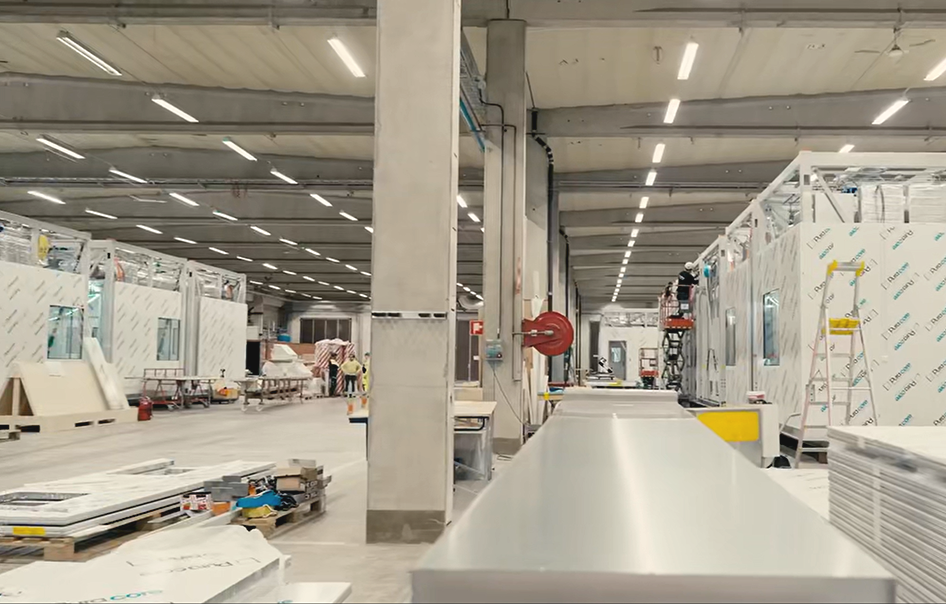
Working as a team for the customer
Working as a team for the customer
When we have visitors, they often comment on the friendliness of our employees and how happy they are to answer questions. Sven, our general manager at the workshop, says that some may expect to see people shouting at one another, but that’s not how things work at the plant.
“The electrical contractor can help our guys, and we can help him; then the ventilation guy can help the electrical guy, because we are all working together trying to work as efficiently as possible for the company. This teamwork is key to our success in offsite modular construction. We’re proud of the fact that we can honestly say we're like a family. Everybody talks to one another, not behind their backs. And everybody feels needed, from the person who cleans the toilets, up to me as the general manager.”
Open discussions are held every month, preventing rumours from gaining a foothold. “When everybody knows everything, it’s much easier,” Sven says. “It’s something we are very proud of, and customers can see it and feel it, especially when they experience our offsite modular construction process firsthand.”
Employees with decades of experience
This open and friendly work environment is one reason why some employees spend their entire careers at the plant. Some of Emtunga’s employees have been working there since the 1980s. One man, who had been working there since 1982, recently retired. “We have people who have been working with modular fabrication for decades. They've set up our modular solutions in more than 30 countries all over the world,” Sven adds.
Because word about this kind of atmosphere gets about, Emtunga never has to advertise when it needs to hire additional staff. “People come to us to ask if they can work here,” says Sven.
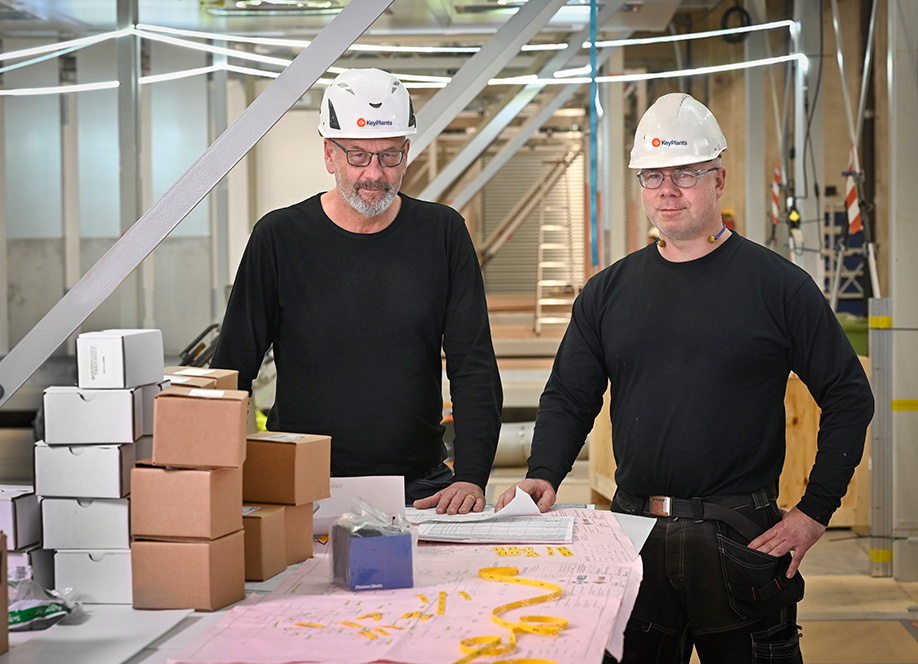
Who we are
At KeyPlants, we take pride in our people, our expertise, and the strong relationships we’ve built with our clients over the years. Our success is driven by a shared commitment to innovation, teamwork, and delivering exceptional results for every project.
Our team at the workshop
For more than 40 years, our employees have been coming up with a wide variety of solutions to many different challenges, learning something from every project along the way. Staff turnover is extremely low, which says alot about the work environment that's been created here. Motivation to deliver great work is high, and our workforce gets stronger and smarter with every passing year.
Our customers
Visitors to our workshop in Emtunga can't fail to notice the friendliness of our employees and contractors, and how happy they are to answer questions. This attitude provides the foundation for great teamwork, facilitatiing the sharing of experience and knowledge to solve whatever challenges come up on a project. And it means we all work together to execute projects as efficiently as possible for our clients. We’re also proud of the fact that we are like a family, and you will see it and feel it when you visit.
Our workshop
We mainly focus on the life science industry, but we also build modules for other markets. Visitors to the 50,000-m2 Emtunga plant in Sweden will be greeted by the friendly faces of about 100 employees and subcontractors, in an immaculate workshop. This comes as no surprise to anyone, as mutual respect and attention to detail are important to all who work here.
The KeyPlants team
KeyPlants experts have end-to-end skills, from design all the way through to final commissioning and qualification, and are capable of carrying out all design disciplines in-house. So, your facility will be designed by some of the best minds in the business before it's even built. End-to-end expertise also ensures smooth handovers at every stage, and a total solution that not only works, but is is delivered on time. All KeyPlants teams are led by widely recognised names in the life sciences industry, and they collaborate with each other every day in closely integrated groups.
Offsite modular construction: A smarter approach
Offsite modular construction is at the core of what we do at KeyPlants. By completing up to 85% of the work in our controlled workshop environment, we ensure consistent quality, reduce on-site disruptions, and speed up project timelines. This approach not only minimizes risks but also allows us to deliver tailored, high-quality solutions that meet the exact needs of our clients.
Our dedicated team in Emtunga combines decades of expertise with cutting-edge techniques to fabricate modules that exceed industry standards. Whether designing for the life sciences industry or other specialized markets, offsite modular construction enables us to maintain precision and efficiency every step of the way. Visitors to our workshop often notice how seamlessly our team works together to make this innovative construction method a success.
Good teamwork, good knowledge transfer
Given the wide range of possible client solutions, it's a key competitive advantage to have long standing employees with vast experience of adapting to clients' needs. Motivated employees who enjoy working as part of a team are invaluable in the smooth transference of knowledge from one generation to the next.
“We can see that a lot of our experienced employees are getting close to retirement, so we try to have our younger people work side-by-side with them on the production line and go to sites together, so we can transfer all that knowledge to the younger generation,” Sven says.
He adds that one challenge is to teach the younger ones to stop using their phones during the breaks and talk to one another instead. “Just like in the old days,” he says with a smile. “To talk face-to-face, instead of just looking at social media or something. It's a tricky thing, but we try.”
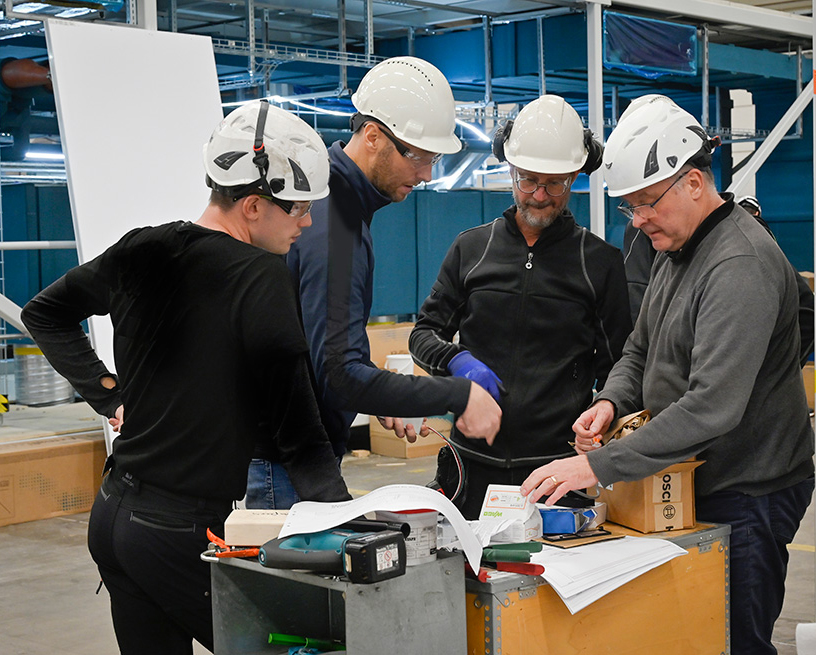
Offsite modular fabrication: A better bottom line
Offsite modular fabrication: A better bottom line
For Sven, what makes Emtunga a special place to work is also what makes KeyPlants special. “It’s the way modular solutions can save time for the customer,” he says. “Compared to a conventional build, modular can save 10 months or more of production time.”
“For example, a big pharma company that's just developed a new drug has 10 years to do it by themselves with patent protection. Then other companies can start to copy that drug. So, that 10 months gives that particular company a lot of extra time with patent protection.”
A safer way to work
A safer way to work
By working in a tidy workshop, risks associated with the outdoors, particularly the weather, are avoided. “We are working in a temperature-controlled area where everything is clean,” Sven says. “When you are working inside, you don't have any problems with snow, or rain, or thunderstorms, or anything like that.”
“And we have great safety procedures. If you work above 1.5 meters off the ground, you have to be hooked up to safety lines to reduce the risk of EHS damage, or lost time injuries (LTI). This means that we have had a very, very low rate of LTIs over the years.”
“At the end of the day, we want people to go home to their families in the same shape they were in when they came to work in the morning.”
It’s this management attitude that has played a big part in motivating the workforce.
Our production site in Emtunga is certified according to ISO 9001:2015, 14001:2015 and ISO 45001:2018.
This means that the production site is certified according to international standards for certification of environment and quality management systems used in companies.
The certification proves that our management systems live up to international standards, have good processes in place and shows that we promote continuous improvement work within the organization. We want to constantly develop and deliver the best products in the most resource-efficient way. The certification is proof for all those who work with or for us, to see that we systematically work with continuous improvement and development.
ISO 9001: 2015 Certification – Quality
An ISO 9001 certification shows that KeyPlants produciton site in Emtunga is dedicated to systematically improving its quality and exceeding its customers’ expectations. As a customer, you know that your partner is in order.
ISO 14001: 2015 Certification – Environment
An ISO 14001 certification shows that KeyPlants production site in Emtunga lives up to concrete and recognized environmental requirements. We take responsibility for the environment towards customers, staff, owners and other stakeholders.
ISO 45001: 2018 Certification – Occupational Health & Safety
An ISO 45001 certification shows that KeyPlants production site in Emtunga is has taken a significant step in our continuous commitment to providing a safe and sustainable work environment. It aims to reduce workplace injuries and illnesses while promoting and protecting both physical and mental well-being.
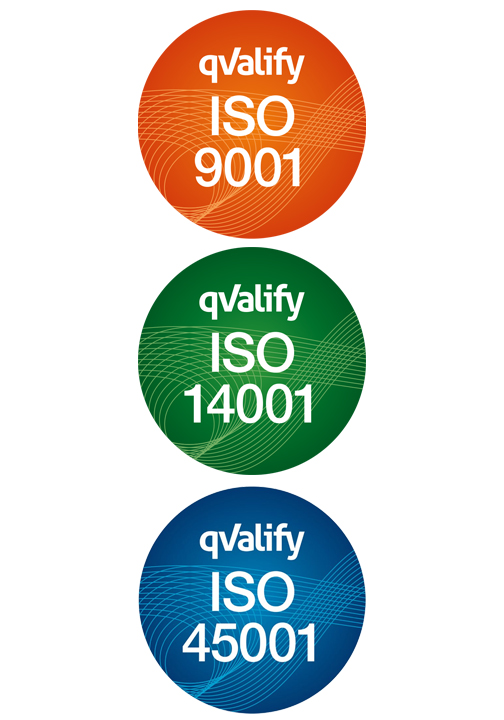