Reference PROJECTS
Pasteur Institute of Dakar: First-of-its-kind vaccine manufacturing facility in Africa
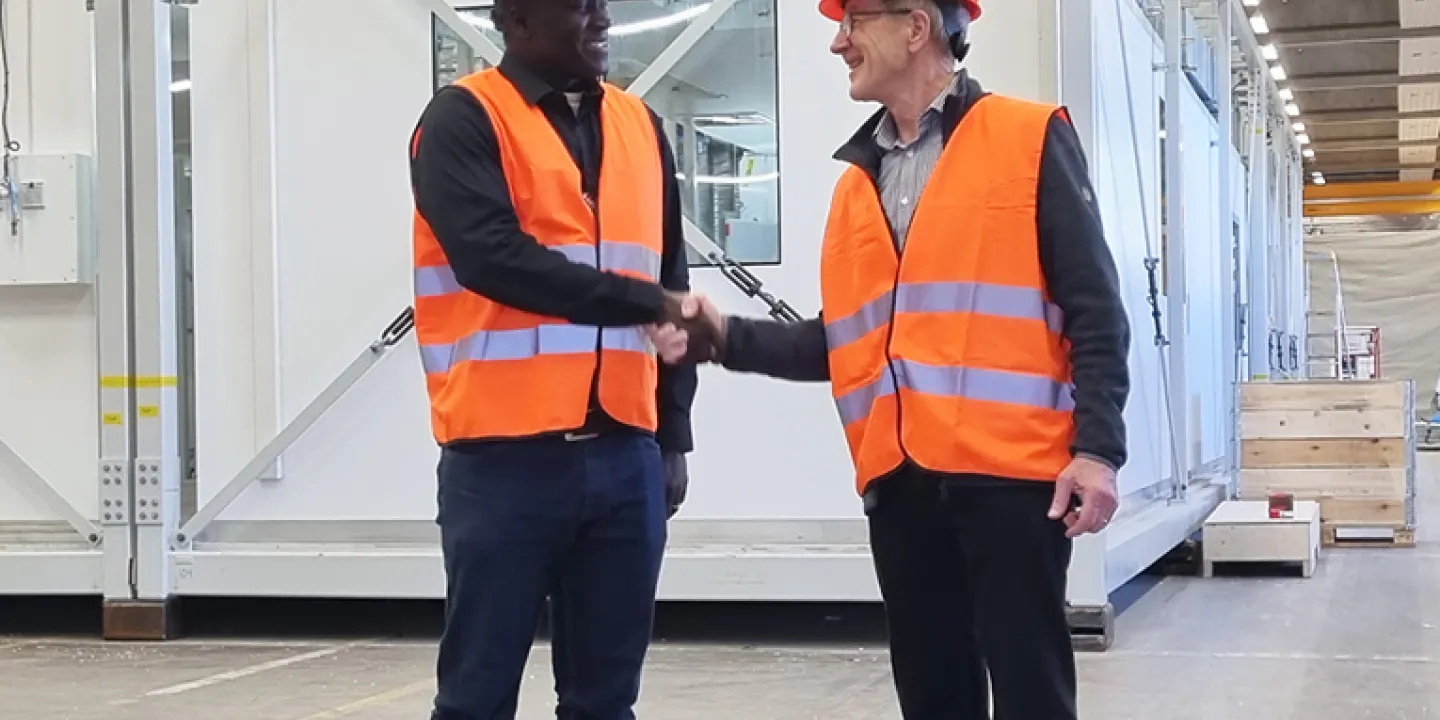
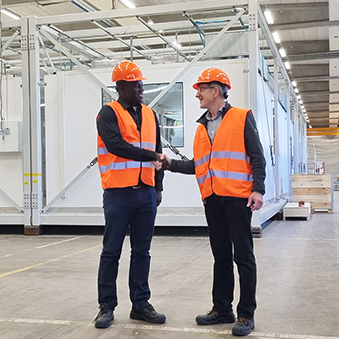
Project details
Project details
Client
Pasteur Institute of Dakar
Location
Africa
Market
Biologics
Solutions we provided
Modular aseptic filling facility for COVID-19 vaccine, indoor modules
Driving self-sustaining COVID-19 vaccine solutions in Africa
Driving self-sustaining COVID-19 vaccine solutions in Africa
Our team at KeyPlants, together with a group of international companies, funders, and governments, have designed and built a first-of-its-kind vaccine manufacturing filling facility in Senegal. Project MADIBA leveraged our unmatched expertise and vast experience in modular solutions and off-site manufacturing to develop this transformative facility in under a year. Owned and managed by the Pasteur Insitute of Dakar, the facility revolutionises access to vaccines in Africa.
What can the Project MADIBA facility achieve?
This facility has the capacity to produce 300 million COVID-19 vaccine doses annually. Its multi-suite drug substance and fill-finish capabilities also mean it has the flexibility to facilitate processes across the pharmaceutical and biomanufacturing industries, beyond mRNA vaccine manufacturing. As a result, it can enable rapid vaccination of the Senegalese population and neighbouring countries against COVID-19, while offering the flexibility to meet changing pandemic and global health needs. The portable, prefabricated design of the facility also allows for a rapid, low-risk scale-up or scale-out process to meet evolving needs of the local community.
Project MADIBA’s mission
This pioneering project aims to implement a self-sustaining and reactive vaccination infrastructure in Africa, taking the first step towards the continent’s goal of vaccine autonomy. It serves as a blueprint for future vaccine manufacturing facilities to be built across Africa. With off-site construction reducing risk and eliminating the need for complex assembly logistics on site, this project proves that any location in the world can now have access to crucial biomanufacturing facilities that produce life-saving medicines.
Project MADIBA’s Journey
Project MADIBA’s Journey
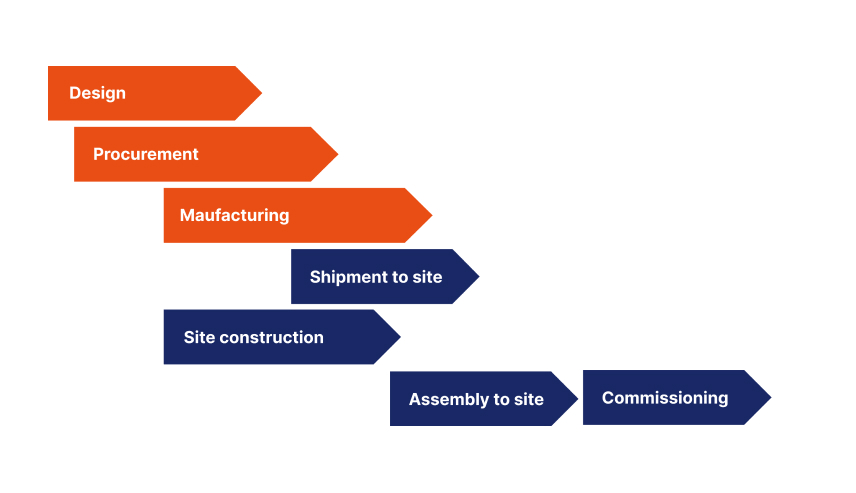
"Through the MADIBA project, the Pasteur Institute of Dakar and its partners are responding to the COVID-19 pandemic by achieving equitable access to life-saving vaccines for Africans. KeyPlants has contributed crucial experience in off-site module manufacturing, enabling us to open an innovative manufacturing facility in Senegal in record time."
Dr. Amadou Sall, Director, Pasteur Institute of Dakar
1. Design
2. Procurement
3. Manufacturing
4. Construction
5. Shipping
6. Assembly on site
7. Commissioning and Qualification
The facility’s design draws upon our vast experience in the industry and our extensive portfolio of previous projects, as well as the need to meet stringent regulatory standards.
During this phase, our specialised team at KeyPlants handle complex procurement interactions with vendors and integrate elaborate process equipment systems
By choosing off-site construction, there is the opportunity to apply sustainable and controlled practices in a safe environment, ensuring the highest regulatory and sanitary standards are maintained.
While KeyPlants design and build the facility off site, IPD prepare the site, build the foundation, and construct the shell building in parallel. This saves time further down the line.
After the facility is fully manufactured in Sweden, it is disassembled and transported to its intended location of Diamnadio, Senegal.
The facility will then be reassembled on site by a swift and specialised installation and commissioning KeyPlants team in collaboration with local teams.
In this step, the facility is verified for performance and engineering requirements. Personnel are trained to ensure product quality reliably meets regulatory and GMP standards.
1. Design
The facility’s design draws upon our vast experience in the industry and our extensive portfolio of previous projects, as well as the need to meet stringent regulatory standards.
2. Procurement
During this phase, our specialised team at KeyPlants handle complex procurement interactions with vendors and integrate elaborate process equipment systems
3. Manufacturing
By choosing off-site construction, there is the opportunity to apply sustainable and controlled practices in a safe environment, ensuring the highest regulatory and sanitary standards are maintained.
4. Construction
While KeyPlants design and build the facility off site, IPD prepare the site, build the foundation, and construct the shell building in parallel. This saves time further down the line.
5. Shipping
After the facility is fully manufactured in Sweden, it is disassembled and transported to its intended location of Diamnadio, Senegal.
6. Assembly on site
The facility will then be reassembled on site by a swift and specialised installation and commissioning KeyPlants team in collaboration with local teams.
7. Commissioning and Qualification
In this step, the facility is verified for performance and engineering requirements. Personnel are trained to ensure product quality reliably meets regulatory and GMP standards.
Now, vaccine manufacturing can begin!
Now, vaccine manufacturing can begin!
Facility in focus
Facility in focus
The Project MADIBA facility is a filling facility capable of filling both vials and pouches due to the use of MEDInstill’s novel INTACT™ pouch technology. The pouch connects to its multi-use injector which will deliver 200 doses of the COVID-19 vaccine to patients without losing container closure integrity and having zero exposure to critical surfaces, while an individual needle for each patient prevents any risk of cross-contamination between patients. Thus, the facility is able to achieve improved high-throughput vaccine manufacturing capabilities safely.
Daniel Py, CEO and Founder of MEDInstill says “With the adoption of MEDInstill’s technology, Project MADIBA will be both transformative and disruptive in the Pharma and Biopharma space by delivering vaccines to those in need at an unmatched safety level.”
Also, the simplified procurement process and prefabricated design of the facility means it is easily reproducible. It therefore provides a safe, rapid, and scalable solution to meet biomanufacturing needs.
Watch our video to learn more about the facility, developed as part of Project MADIBA and in collaboration with the Pasteur Institute of Dakar (IPD) and Medinstill.
KeyPlants, a leading provider of innovative life science facilities
KeyPlants was chosen to execute the ambitious goal of Project MADIBA due to our unrivalled experience in successfully designing, manufacturing, delivering, and commissioning over 4,500 off-site modules to customers worldwide. The controlled production environment means that safety always comes first for us.
In combination with our vast understanding of the industry and integrated supply chain control, this positions KeyPlants as a reliable partner who can mitigate project risks and meet tailored biomanufacturing needs in short and predictable timelines. At KeyPlants we provide turnkey solutions, no matter the scale of the project, to ensure drugs reach patients faster.
KeyPlants is part of Masco Group, a family of companies that deliver integrated projects to support its customers manufacturing in the pharmaceutical and biopharmaceutical space.
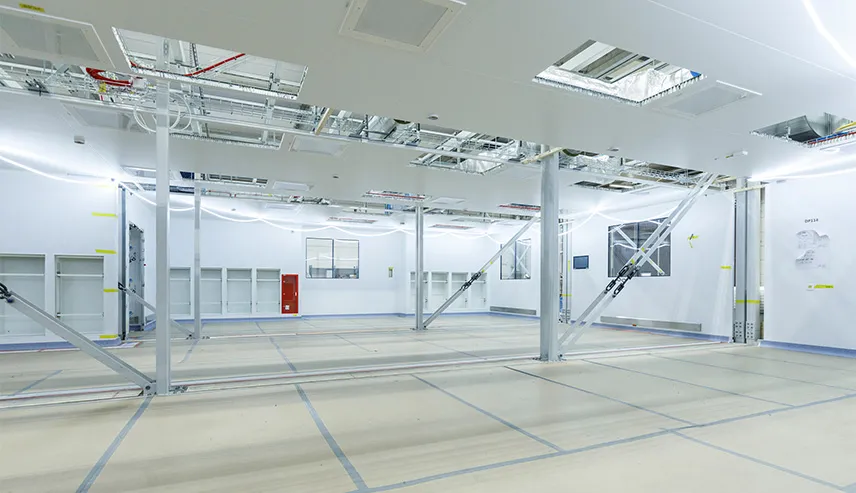
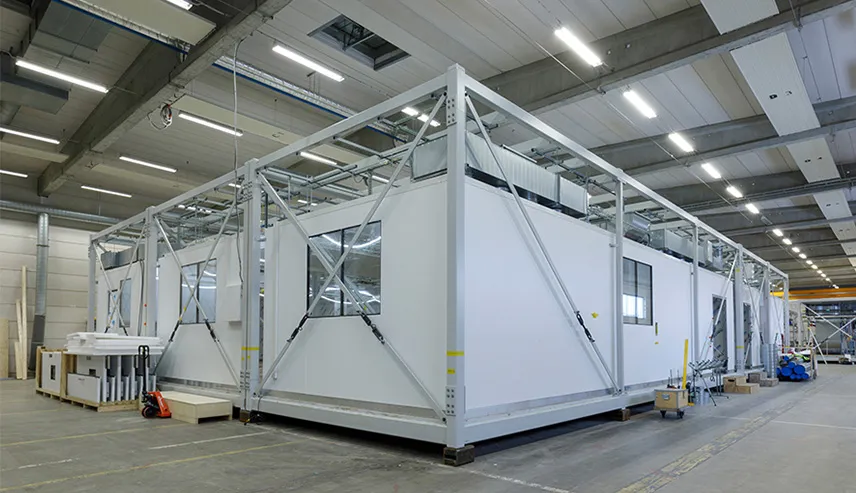
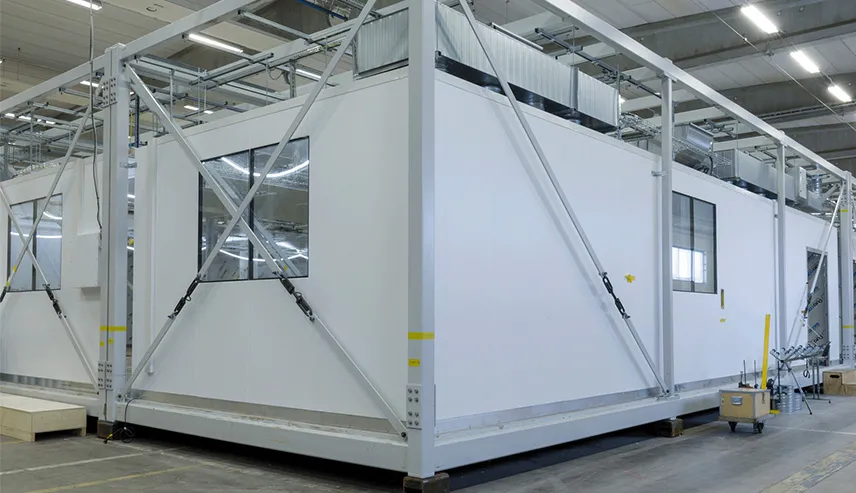

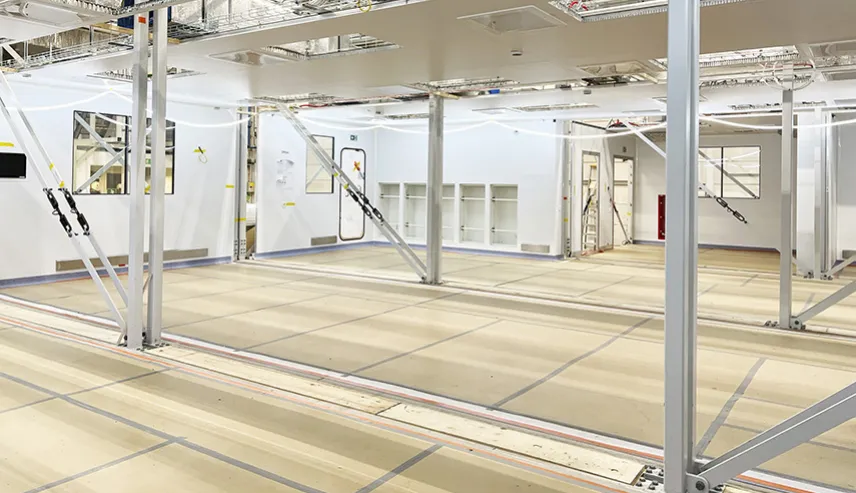
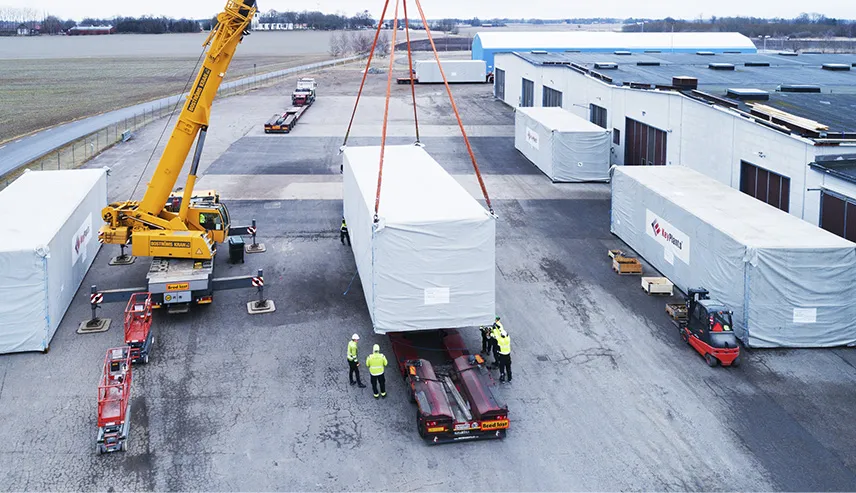
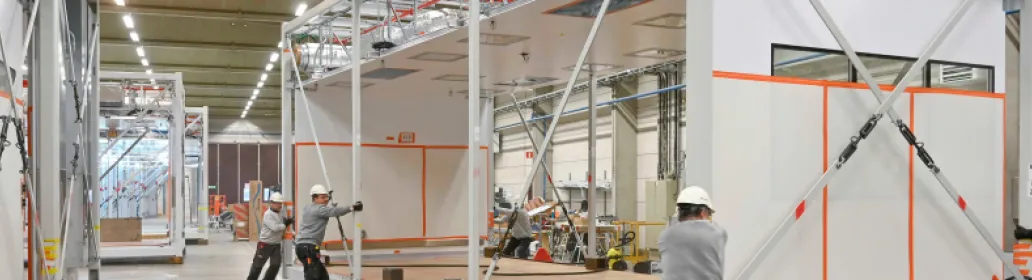