Reference PROJECTS
Offsite Construction Accelerate Batavia's Biopharmaceutical Project
Project details
Project details
Client
Batavia Biomanufacturing (CDMO)
Location
Leiden, The Netherlands
Market
Biologics
Solutions we provided
Design, Offsite Construction, Delivery, Installation and Clean Room Commissioning.
The Challenge
The Challenge
Batavia was leasing a new building from a construction contractor and needed to quickly transform the third floor into a state-of-the-art biologics manufacturing environment. The project faced several significant challenges:
• A demanding timeline that traditional construction methods would struggle to meet
• Space constraints at the building site that limited material storage and handling
• Complex coordination requirements between multiple stakeholders
• Precise technical specifications requiring specialized expertise
VILS, a sister company to KeyPlants and the contractor responsible for the interior fit-out, decided that a hybrid build including a modular approach for one floor with offsite construction would be crucial to addressing these challenges and called on KeyPlants.
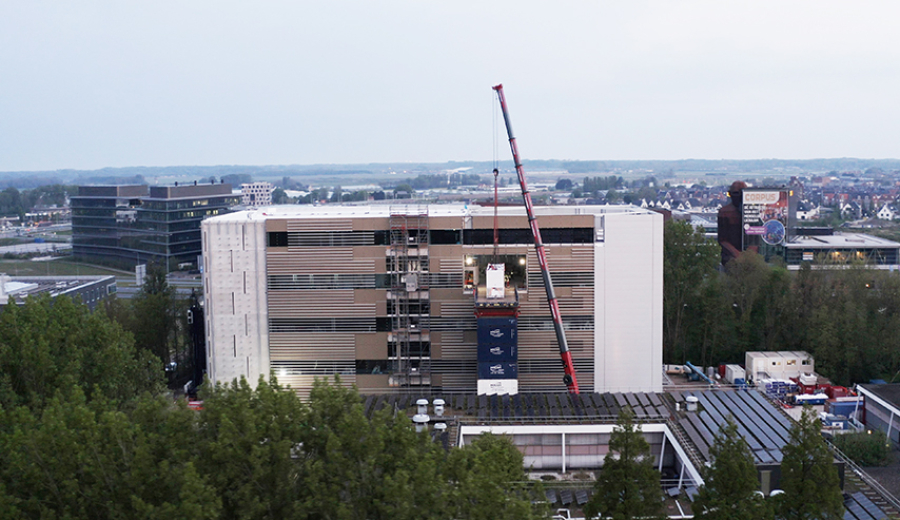
The KeyPlants Solution
The KeyPlants Solution
KeyPlants executed the design prefabrication in Sweden, transported the facility to the site in Leiden and completed the installation and commissioning on site.
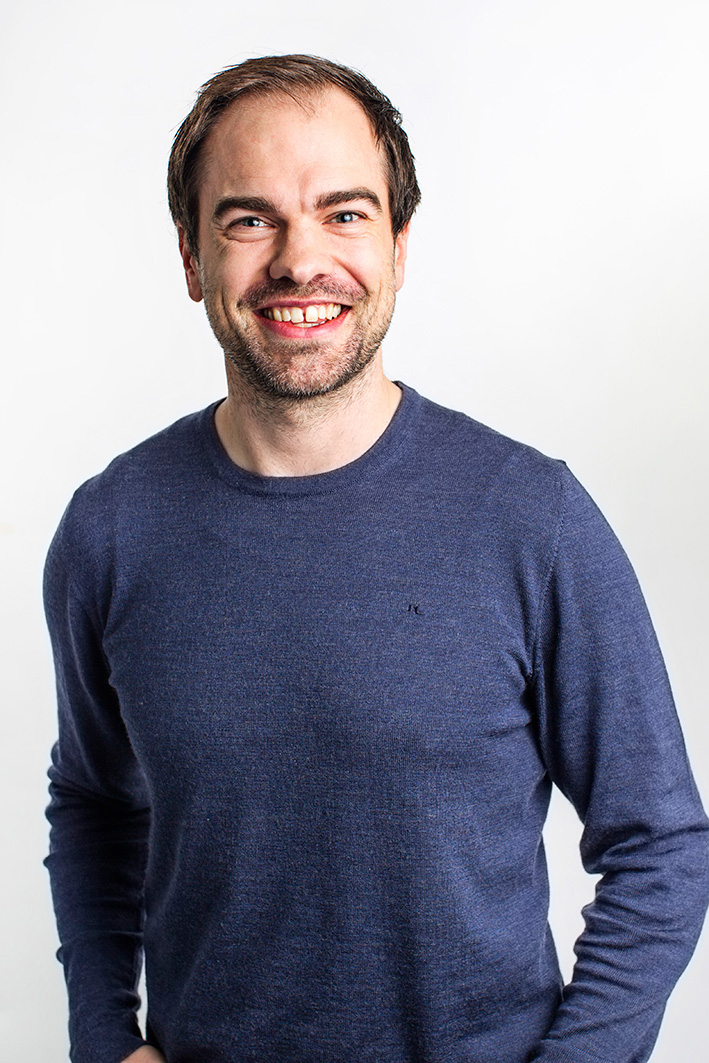
Parallel Construction
The offsite manufacturing approach provided several crucial advantages that helped meet the project's demanding requirements, starting with parallel site construction. While site preparation work was underway at the building, KeyPlants was simultaneously manufacturing the modular facility in their workshop in Sweden. This compressed the overall timeline significantly compared to sequential on-site construction.
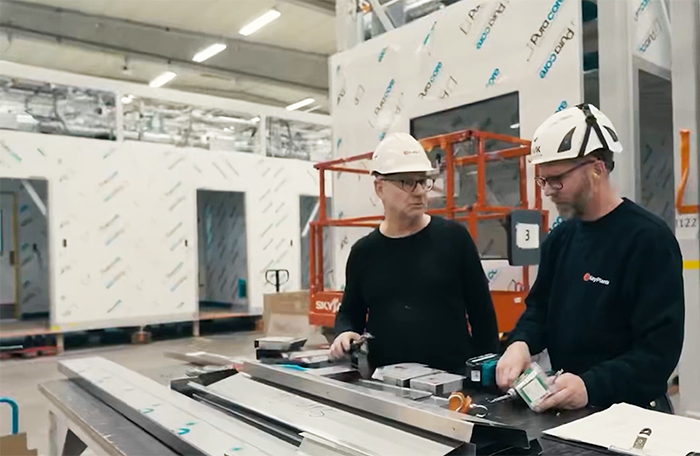
Reduced Logistical Complexity
Reduced Logistical Complexity
Instead of managing hundreds of material deliveries to a constrained site over many months, this approach required only a few number deliveries from Sweden to the Netherlands over approximately three weeks.
“If you would build everything conventionally, you would have to have just-in-time deliveries of all materials because you couldn't store materials on site," noted Pettersson. "I don't even know if it would be possible to have all that material on site that was needed to build the cleanrooms on floor 3.”
Enhanced Safety and Quality Control
Enhanced Safety and Quality Control
Factory construction allowed for better quality control and safer working conditions than would be possible with on-site construction.
"From a safety point of view, we could lift in our modules and then work in the modules where most of it is prefabricated," Pettersson explained. "If you would have to manage all those materials and all those lifts and transports every day, that would be a huge risk."
Olle Pettersson, Project Manager at KeyPlants
Minimized Weather Impacts
Minimized Weather Impacts
Although the project did experience a brief one-day delay due to high winds during module installation, this represented a fraction of the potential weather-related delays that conventional construction might have faced with daily material deliveries over many months.
Image
![]() | Image
![]() |
Simplified Project Management
Simplified Project Management
The modular offsite construction approach aligned perfectly with VILS' project management strategy, which sought to consolidate work into manageable packages. Instead of managing 20 or 30 different subcontractors, VILS combined activities among a few partners of which KeyPlants represented a major part. This allowed VILS to maintain better control and achieve faster execution, with smoother coordination between different contracts, timelines, and milestone requirements.
“It was a big benefit because they could have one work package for the production areas and KeyPlants could take care of it," says Pettersson. "We also didn't have a lot of coordination issues with VILS because we could independently do a lot of our work.”
Technical Innovation
Technical Innovation
The project required significant technical innovation, particularly in the design of the module floors. To ensure seamless integration with the existing building floor, KeyPlants developed an unusually thin floor system of just 4 centimeters, ensuring that no ramp would be required to roll in material and mobile equipment from the corridors into the facility.
Collaborative Approach
Collaborative Approach
Despite initial challenges with coordination between multiple stakeholders, the project team developed strong working relationships that contributed to the project's success.
“We've had a very solution-oriented collaboration together," Pettersson said of the relationship with VILS. "If we had problems, the main focus was on how we could solve those together.”
The KeyPlants team's extensive experience—with some installation team members having over 30 years in the field—also proved invaluable in addressing unforeseen challenges as they arose.
Results
Results
Today, Batavia has a fully operational, high-quality biomanufacturing facility that meets all requirements. The project demonstrates how offsite construction, when properly applied, can help overcome the challenges of complex facility projects even in constrained environments.
The successful collaboration between VILS as the main contractor and KeyPlants demonstrates the power of combining complementary expertise to deliver exceptional results for clients.
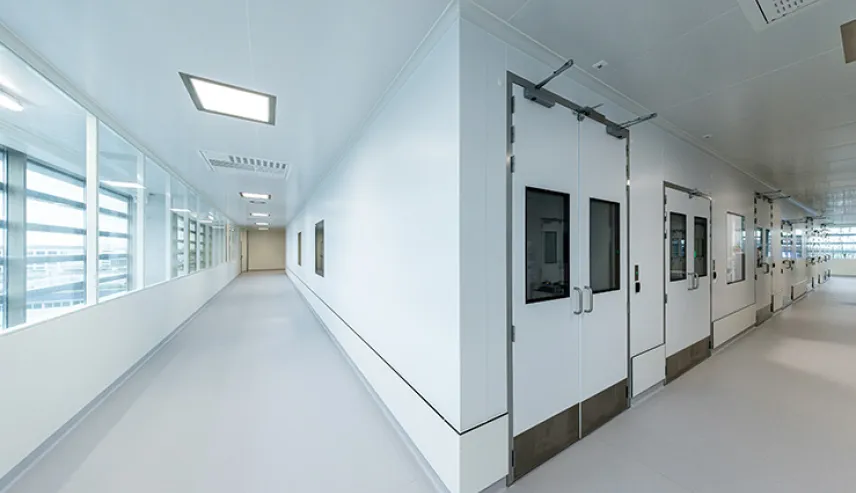
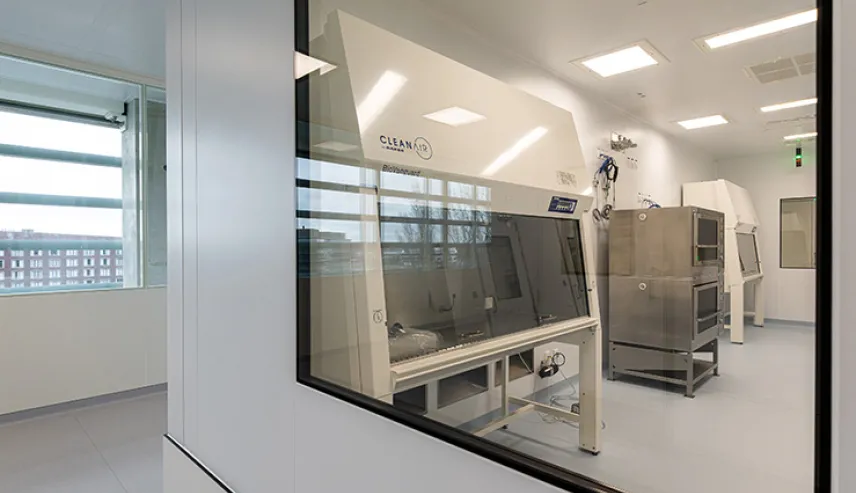
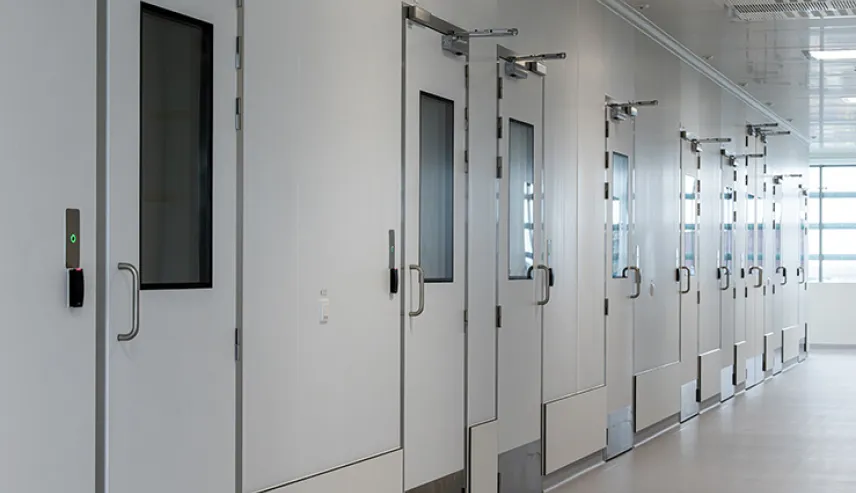
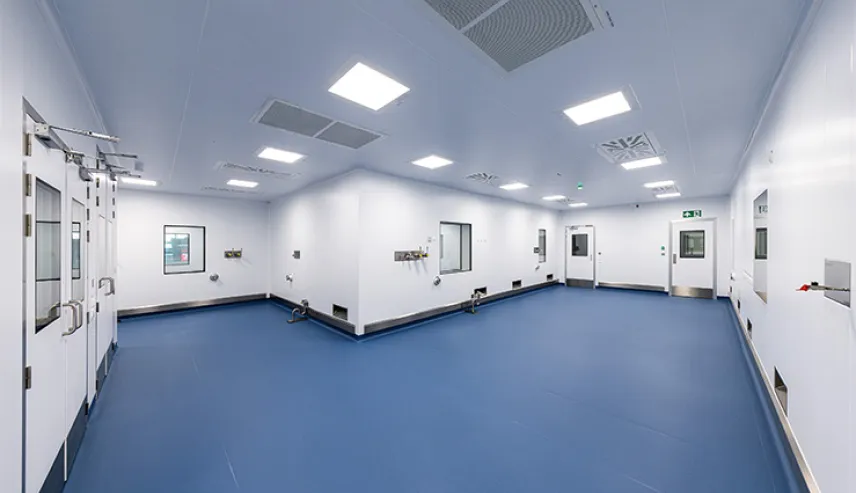
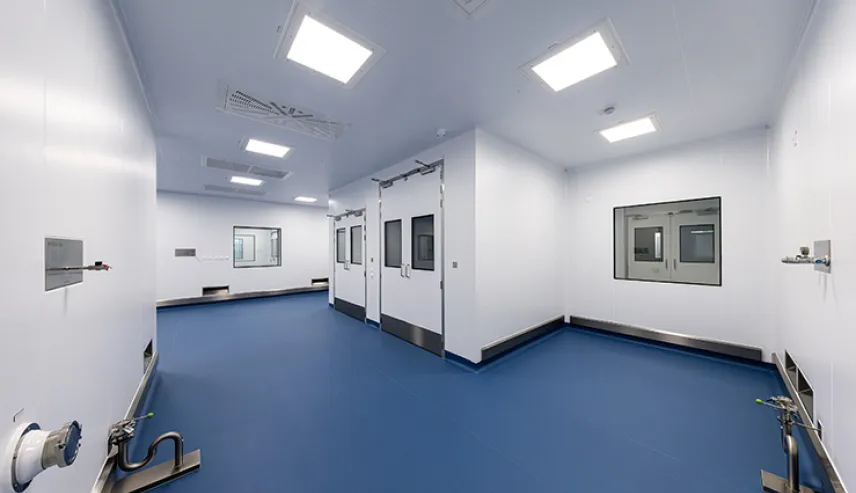
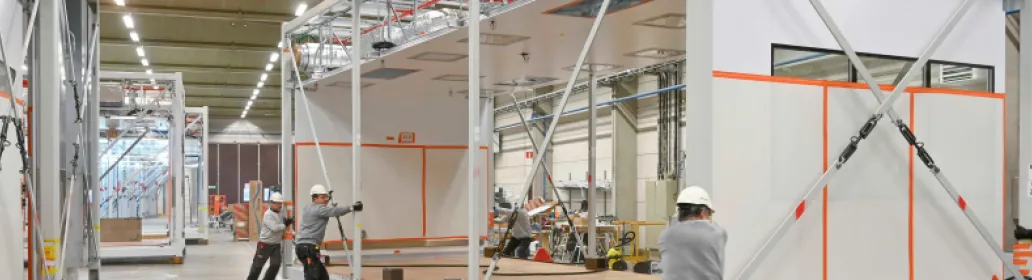