Reference PROJECTS
Automating cleanroom HVAC system to meet sustainability goals
Project details
Project details
Client
Maker of implant coatings
Location
Sweden
Market
Medtech
Solutions we provided
Automation of cleanroom HVAC system to reduce airflow and save energy outside working hours while maintaining cleanroom and employee safety standards.
Automating cleanroom HVAC system to meet sustainability goals
Automating cleanroom HVAC system to meet sustainability goals
When a Swedish maker of coatings for implants sought to align its operations with its ambitious sustainability goals, it turned to KeyPlants for help achieving them. KeyPlants delivered energy savings by automating the company’s cleanroom HVAC system to reduce airflow during unoccupied hours – while maintaining the stringent standards required for medical production.
The solution, designed and implemented by KeyPlants, combines sustainability with operational flexibility, cutting airflow to 20% of its full rate during off-hours without compromising cleanroom integrity.
The client chose KeyPlants for this project because of its deep familiarity with the facility. As the original designer and builder of the cleanroom and its HVAC system, KeyPlants was uniquely positioned to deliver an innovative and precise solution.
This project also reinforced the strong collaborative relationship established during the initial construction of the facility—a complex endeavor involving multiple contractors and disciplines: ISO Grade 7 Cleanroom Solution Optimises Production Flow.
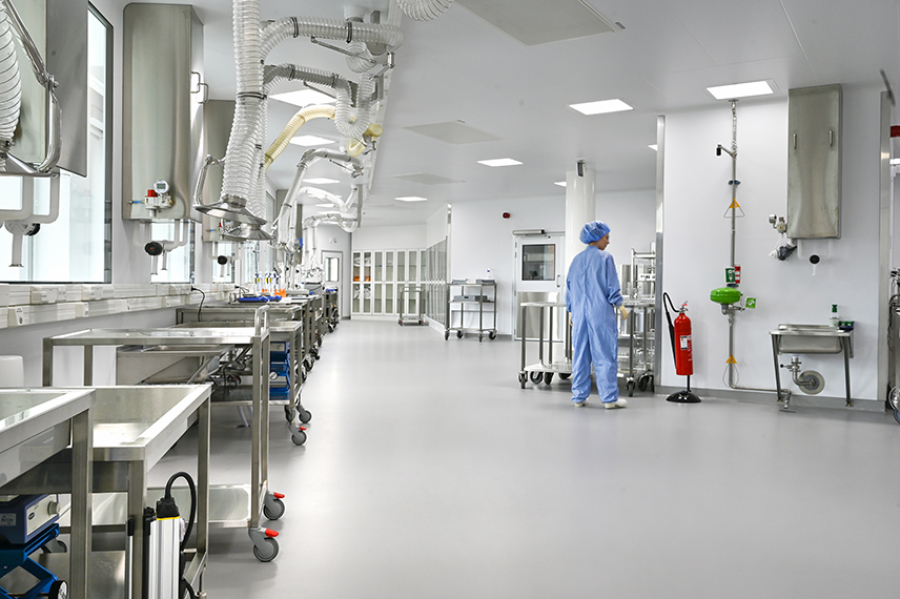
Facility Details
The facility, which employs about 60 people, is dedicated to the production of high-quality medical materials, including coatings for implants and a heparin-based substance used in blood-thinning medications. The cleanroom, designed and built by KeyPlants, plays a critical role in ensuring product quality and compliance with strict regulatory standards.
The cleanroom’s HVAC system is a subsystem within the facility’s broader HVAC infrastructure.
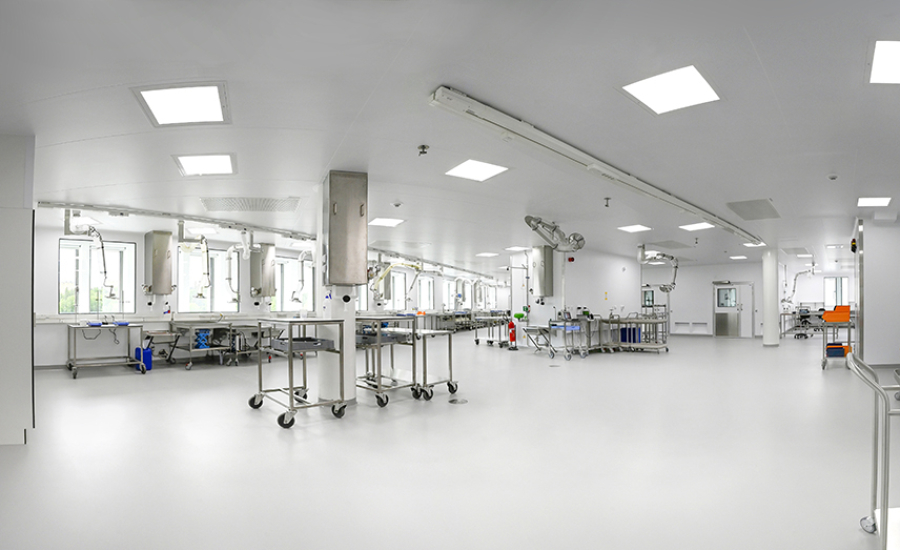
As Peter Rylén, Senior Automation Engineer at KeyPlants, explains, “The air is supplied from the main system, but we filter and condition it specifically for the cleanroom to maintain the correct temperature, humidity, and differential pressure.”
Sustainability and Innovation
At first glance, reducing airflow during unoccupied hours to save energy seems straightforward. However, achieving this without compromising cleanroom standards required careful planning and execution.
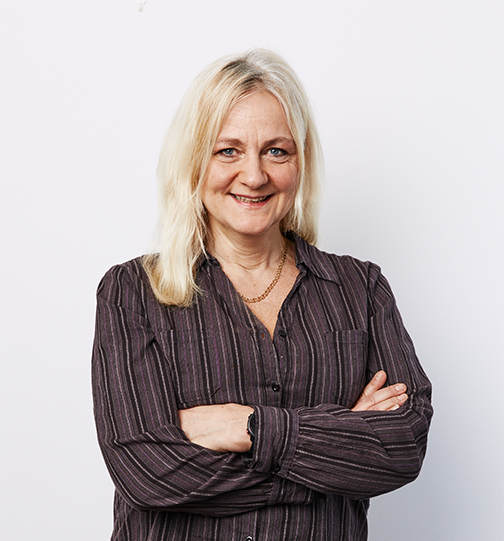
To accommodate employees working outside normal hours, the system includes an override feature. “If someone works late, they press a button to delay the reduced airflow, and there’s an alarm to remind them the change is coming,” Stattin adds. This approach balances sustainability with operational flexibility, reducing airflow to 20% of the full rate during unoccupied hours while maintaining cleanroom standards and worker safety.
Challenges and Solutions
Challenges and Solutions
While the concept of reducing airflow to save energy is simple, execution was far from easy. One of the key challenges was maintaining the correct overpressure in the cleanroom while transitioning between full and reduced airflow rates.
This required a multidisciplinary effort, involving KeyPlants’ automation and HVAC specialists, as well as close collaboration with the client’s in-house experts. As Rylén notes, “Balancing airflow in and out to maintain the correct overpressure was especially tricky in practice. But through collaboration across disciplines, we found the right solution.”
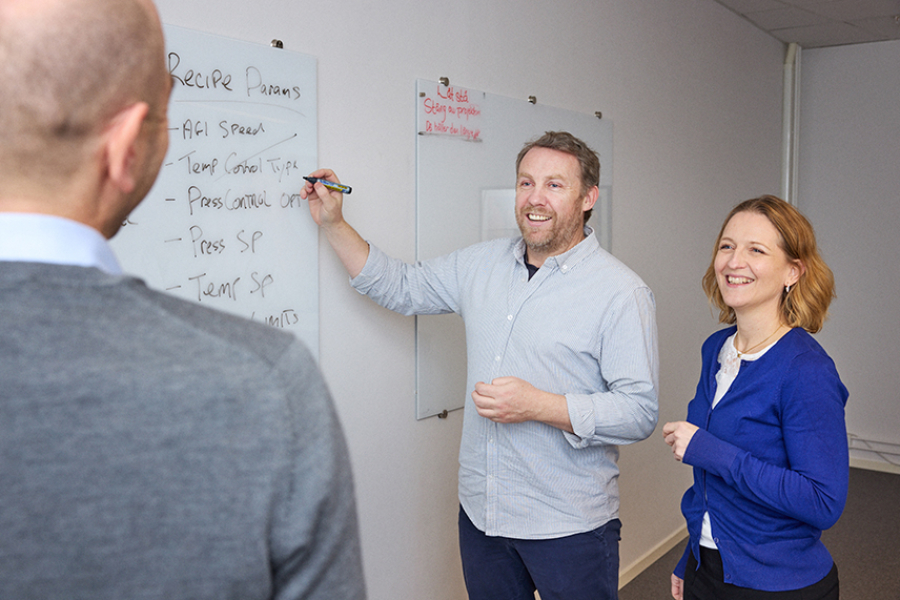
The cleanroom’s design also accounts for strict particle control, which must operate 24/7. “Even people walking inside the cleanroom generate particles,” Stattin points out. “Workers are trained to move slowly, and systems like this must ensure the environment remains clean."
Partnership Success
The success of this project hinged on KeyPlants’ expertise and the strong partnership with the client. “The client was a great partner—helpful and understanding,” says Rylén. This collaboration extended beyond the project, with KeyPlants now providing ongoing support for system updates and improvements.
This project underscores KeyPlants’ ability to deliver innovative, sustainable solutions while maintaining the precision and quality required in cleanroom environments. By working closely with the client, KeyPlants achieved a solution that not only met operational needs but also supported the client’s commitment to sustainability.
Through its tailored approach and deep expertise, KeyPlants continues to help clients achieve their goals, whether it’s building state-of-the-art facilities or optimizing existing ones for greater efficiency and sustainability.
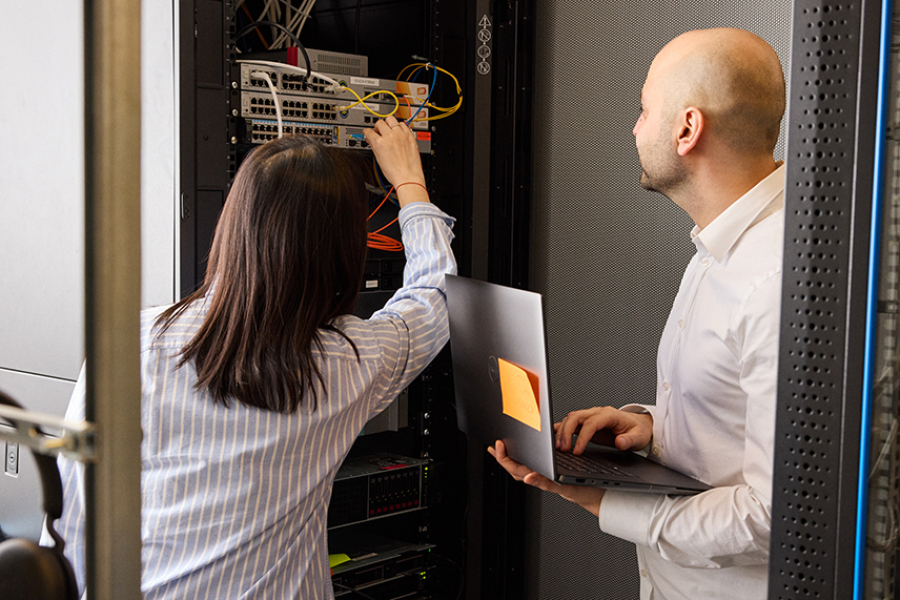
