TURNKEY PROJECTS
Offsite Modular Design and Construction
Offsite construction lower cost and risk, while increasing quality, safety and speed
Offsite construction lower cost and risk, while increasing quality, safety and speed
Are you thinking of expanding your production? Or launching a new product? At KeyPlants, we have decades of experience building modular, turnkey facilities for the world’s leading pharmaceutical and biotech companies. Our modular agile design solutions meet the demanding requirements of today’s business needs in the production of therapeutics. And by deploying standardised, repeatable facilities globally, you can reduce variability from project to project, and reduce both cost and schedule, from the design process to fabrication and startup. It's why so many companies choose KeyPlants for their facility projects.
Pods cut lead times to weeks
Our portable on-demand (pod) facilities dramatically reduces the time it takes to set up new production, speeding up the development of cutting-edge therapies, and increasing production flexibility. pods can be on site and ready for operation anywhere in the world, in just few weeks for a single pod, compared to a year or more to build a conventional facility from scratch. They also offer maximum flexibility in production. pods give manufacturers:
- flexibility to start small-scale production immediately and then scale out
- the advantages of a fixed price and time schedule
- a turnkey, integrated approach instead of pieces of a facility/process engineering puzzle
- an end to the time and complexity of specification, bidding, procurement, and permitting
- lower total cost of ownership (TCO)
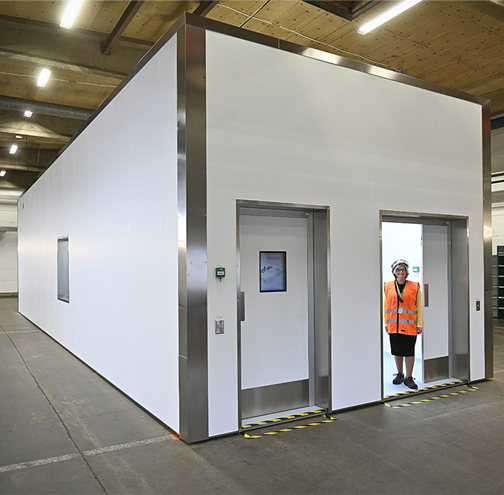
Flexible solutions for evolving production needs
Pods are the fastest way to start or expand production, which will result in innovative, cost-effective solutions, from clinical development to commercialisation, since the total cost of ownership will be reduced. pod facilities can be sized-up by adding pods, and are also a solution for the small-scale production of cell and gene therapies, for example.
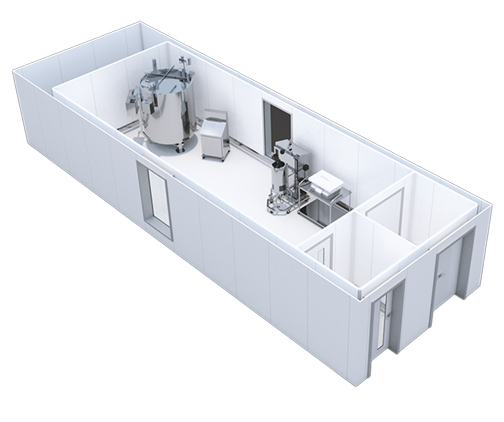
Modular process skids
We design, fabricate, install and qualify speciality modular process skids and systems for:
- Aseptic formulation, holding and filling of liquids
- Systems for the deriving of products from human plasma
- Media and buffer preparation skids
- CIP and SIP Skid Units
- WFI tanks skids
- Mobile Vessels
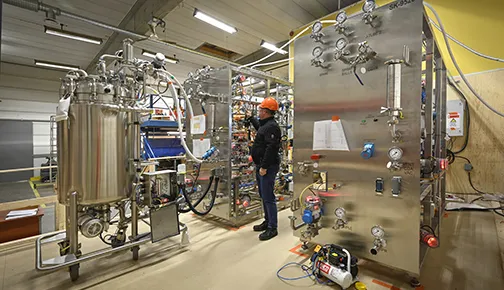
Offsite construction benefits
Offsite construction benefits
Reduced cost
We all know that modularization of process modules, pipe racks, facility modules, cleanroom panels etc., increases predictability and reduces cost overruns. It also shortens the delivery time, leading to a faster return on investment.
There are several reasons for this. Manufacturing processes are evolving rapidly, with labour productivity increasing by more than 150% in the past 50 years. At the same time, conventional construction productivity has fallen by nearly 20%.
Modular manufacturing off-site allows more re-use of proven solutions and minimises the need to reinvent.
Efficient manufacturing workflows reduce time spent on preparation, getting materials, instructions and making up for errors etc. Indeed, 88% of a worker’s time is spent productively. Good teamwork, with no middleman involved in the modular manufacturing part of the project, only serves to help.
Construction industry productivity has dropped by 19% since 1964, but it has increased in tracked industries by 153%.
Modular Manufacturing:
Spend less, earn more
With modular manufacturing, there’s little difference between the estimated costs at the concept design stage and the actual costs when production starts. This is one of the big advantages of modular manufacturing. It involves less risk. So, what are these risks? They include schedule risk, cost of capital risk, production risk and revenue risk. And risk costs money. Eliminating schedule risk, cost of capital risk and productivity risk can easily reduce the cost of a project by more than a third.
The bottom line? Modular manufacturing is the fastest way to increase revenues and profits.
Reduced risk
In modular manufacturing,
There’s less to go wrong?
The vast majority of KeyPlants projects meet the planned budget and timelines, with no quality issues to be ironed out or unexpected costs. And when clients want to build a duplicate facility they do not have to start all over; much can be re-used.
Reducing the risk to revenue both from the shorter modular manufacturing timeline and from the lack of delays and quality issues significantly reduces costs compared to conventional construction. KeyPlants’ grid-based standard modular platform design and products let you take control and reduce the risk of the unexpected. Costs can be precisely calculated. Project timelines can be guaranteed. So can process quality. What you see on the drawing board is what you get on your site.
Higher quality and safety
Offsite fabrication in a factory makes the facility less dependent on labor quality, leading to higher productivity, better control of cost and schedule, higher predictability, and higher quality and safety, with substantial testing off-site.
Quality is consistent, because work is carried out by the same skilled workforce and tested in an ISO 9001-certified workshop. And if you decide you want another facility built in another part of the world, we can make a duplicate copy for you; the only variables are sight preparation and labor force building the external shell.
This predictability has bottom-line implications: Your facility will start producing your product on time and much faster than a conventional facility. And that means faster return on your investment.
Increased quality
Off-site manufacturing increases quality and safety.
With our quality management system, we have standard procedures and instructions in place, and these are used for all projects. The quality management system covers the complete project, from design, through procurement and manufacturing, to commissioning and qualification. Relevant, GMP-compliant documentation facilitates our clients’ validation, operations, and maintenance.
Modular manufacturing offsite obviously minimises such variables as differing materials, building codes, construction quality standards, and labour force quality. Fabrication in a factory also makes the facility less dependent on labour quality, leading to higher productivity and better control of costs and schedules.
Safety also improves because so much of the work is carried out in highly controlled factory conditions, instead of out in the field.
Replication and relocation
With offsite manufacturing, if you decide you want another facility built in another part of the world, we can make a duplicate copy for you. The only variables are site preparation and the labour force building the external shell. You also gain full flexibility in changing the location of a planned facility in response to an event.
For example, one client had planned to set up a facility in a Latin American country. But while the modules were being fabricated, political instability there caused concerns. So, the client decided to place the site in Southeast Asia instead.
Increased safety
Working on a building site is one of the world’s most hazardous occupations. This is why maintaining a safe and secure work environment is a key strategic area for us.
We are proud to have substantially reduced risks through effective, systematic work environment management. Our main priority is to ensure everyone returns home in full health at the end of the day, and we devote considerable resources to foster a culture of safety.
The aim is to maintain a workplace that is both progressive and physically, psychologically, and socially safe for every employee, so that the risks of occupational injury and work-related ill-health are prevented. For example, our factory-based employees always carry a safety line if they work high above the ground. We are also committed to maintaining a democratic workplace in which every employee is equal, whatever their role. This creates a safe and secure workplace for us, and a high-quality product for you.
Simplified technology transfer
Off-site manufacturing solves key technology transfer challenges.
Technology transfer is a key challenge whenever setting up new production, whether it’s scaling up from development for a commercial launch of a new product, increasing existing production by building a new facility, or establishing local production to launch an approved product on a new market. Distance, local building regulations, regulatory product approval, and cultural issues are among the hurdles.
Modular manufacturing off-site can be a fast, cost-effective, and low-risk solution for pharmaceutical companies looking to build identical production facilities across Europe, the U.S., and anywhere else in the world. Also, it's useful for companies looking to establish local production in developing countries with limited access to engineering and process expertise.
Streamlines regulatory approval and training
By ensuring identical manufacturing processes, the need for costly and time-delaying clinical studies is avoided, and the regulatory approval process can be streamlined. And with movable facilities, you can easily control the technology transfer process. For example, you can train operators in the location of the new facility, or somewhere close to current operations, or at KeyPlants’ workshop. That’s more effective than performing all tech transfer activities at some distant location.
KeyPlants also has the expertise to carry out off-site fabrication and pre-qualification efficiently, with minimum site disruption, through the rapid deployment of modular, movable facilities.
A compliant regulatory pathway
Limited differences between the existing and new facilities ensure smooth regulatory approval.
Movability
A complete manufacturing facility can be built in one location, further equipped, tested, and qualified in another location, and then moved again to a final site to begin production.
Off-site manufacturing
A complete building can be fabricated, with clean rooms, process equipment, and utilities.
All work is performed under workshop conditions according to agreed specifications.
By performing the tech transfer activities at the original manufacturing site, our clients can benefit from the full expertise and knowledge of their staff, and there’s no loss of information, knowledge, or experience.
With KeyPlants’ off-site modular approach, the facility design and manufacturing can also be conducted in parallel with search, permitting, and preparations at the final site. This further shortens the timeline.
Sustainability
We are constantly striving to improve the way we work to make it more environmentally friendly.
In our search for solutions that are gentler on the environment, we are always seeking ways to develop more sustainable processes and production methods. The challenges are many, but the environment is always on the agenda, helping us stay focused on the issue as we develop our company.
Every year, the quality of our environmental work must be reported and renewed, with new goals for continuous improvement and sustainable development. Below are some examples of the ways we are improving our work in the light of environmental concerns.
We have routines in place to optimise the usage of raw materials, such as steel, so we don’t use more than is necessary in our production process. When possible, we also try to use alternative products.
We constantly monitor and measure waste which arises in production. We sort waste that occurs during the production and renovation of modules, to minimise the waste that must go as landfill.
In the transportation of our modules to different sites, we strive to find ways to reduce emissions.
We also monitor and measure the energy consumption that keeps our business running, as well as being prepared for any emergency that could affect the environment in the event of an accident.
How KeyPlants excels in turnkey projects and offsite modular design
How KeyPlants excels in turnkey projects and offsite modular design
At KeyPlants, we deliver innovative turnkey project solutions designed to meet the unique needs of industries such as pharma, food and beverage, and advanced technologies. Our comprehensive approach ensures that facilities are delivered efficiently, sustainably, and ready for immediate use.
From conceptual design to final qualification, we manage every phase of the project lifecycle. By combining engineering, procurement, modular fabrication, and on-site installation and qualification, we ensure seamless communication, precise execution, and strict adherence to timelines and budgets. This integrated approach guarantees that our clients receive facilities built to the highest standards of quality and performance.
To enhance our turnkey solutions, we integrate offsite and modular design into our projects. Modular units are constructed in controlled environments to ensure consistent quality and precision before being transported for rapid on-site assembly. This method significantly reduces construction time and minimizes disruptions, offering a versatile solution tailored to the specific needs of industries like life sciences, process and advanced technologies.
Pre-Engineered Facility Design Platforms
KeyPlants offers standardized modular design platforms providing maximum flexibility and compliance with industry regulations. Modular Bio Solutions (MBS) and Modular Aseptic Solutions (MAS) are facility solutions designed for biopharmaceutical and pharmaceutical applications where each modular facility is engineered to meet GMP requirements with an optimized footprint and prepared for future expansion.
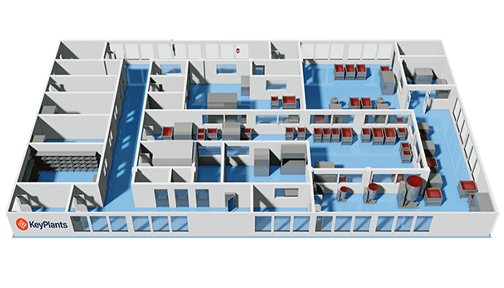
Proven expertise in delivering industry-leading facilities
Our expertise in both turnkey project execution and modular design is backed by a strong portfolio of successful projects. Notable examples include expanding the biomanufacturing capacity at several big pharma sites across Europe and USA and delivering state-of-the-art aseptic filling facilities for vaccine production in the Middle East and Africa. These projects demonstrate our ability to provide innovative, efficient, and sustainable solutions across diverse industries and geographies.
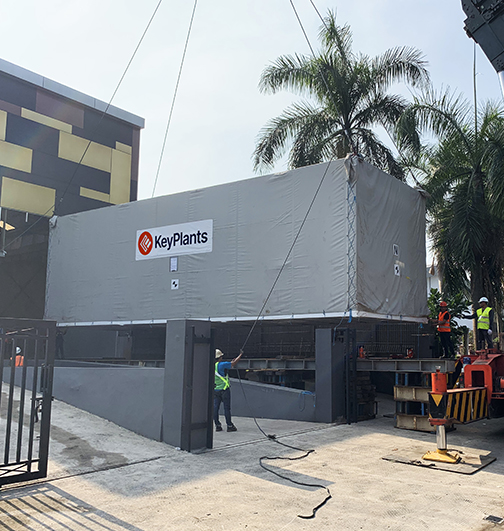
A partner you can trust
A partner you can trust
At KeyPlants, we combine extensive experience in turnkey projects with the advantages of offsite and modular design to deliver facilities that exceed expectations. Whether you operate in life sciences, food and beverage, or another industry, we are dedicated to helping you achieve your operational goals with precision, quality, and sustainability.
Our commitment to innovation and collaboration ensures that each project is tailored to your unique requirements. By leveraging cutting-edge modular technology and sustainable practices, we not only optimize your facility's performance but also minimize environmental impact. With KeyPlants, you gain a partner who prioritizes efficiency, compliance, and long-term success in every solution we deliver.
FAQ
FAQ
What is a turnkey project?
A turnkey project is a type of project where one contractor handles everything—design, construction, and delivery—so the client gets a commissioned ready-to-use facility or system. The client just "turns the key" to start using it.
A turnkey project is a type of project where one contractor handles everything—design, construction, and delivery—so the client gets a commissioned ready-to-use facility or system. The client just "turns the key" to start using it.
What are the benefits of a turnkey project?
Turnkey projects offer several advantages, including streamlined communication since the contractor is the single point of responsibility. They also save time and ensure cost predictability by consolidating the entire process under one management structure. Additionally, clients receive a complete, ready-to-use facility without the need for extensive involvement in the project phases.
Turnkey projects offer several advantages, including streamlined communication since the contractor is the single point of responsibility. They also save time and ensure cost predictability by consolidating the entire process under one management structure. Additionally, clients receive a complete, ready-to-use facility without the need for extensive involvement in the project phases.
Which industries can benefit from turnkey projects?
Turnkey projects are widely used in sectors that require high precision and quality, such as life sciences, food and beverage production, medical devices, and advanced manufacturing. The flexibility of this model allows it to adapt to the specific needs of each industry.
What is offsite modular design?
Offsite modular design is a construction method where facility modules are designed and fabricated in a controlled factory environment before being transported to the project site for assembly. This approach allows for high precision, better quality control, and faster project timelines, as the fabrication process runs parallel to site preparation.
What are the benefits of offsite modular design?
The key benefits of offsite modular design include faster project delivery, improved quality, and reduced risk. By manufacturing modules offsite, construction time on-site is significantly reduced, which minimizes disruptions and allows for faster facility commissioning. The controlled factory environment ensures higher consistency and quality, while costs and risks are better managed compared to traditional construction methods.
Which industries benefit most from offsite modular design?
Offsite modular design is particularly advantageous for industries that demand high precision and strict regulatory compliance, such as life sciences, food and beverage production, medical devices, and advanced manufacturing. These industries benefit from the speed, scalability, and quality control that modular design provides.
Our projects
“Bringing Strategic Generics to new markets requires speed and skills. That’s why Stragen Pharma chose KeyPlants as our partner”
“80% of all conventional projects are delayed by more than four months."
“KeyPlants took responsibility from project start to implementation. A successful delivery, on time, with a tight schedule.”
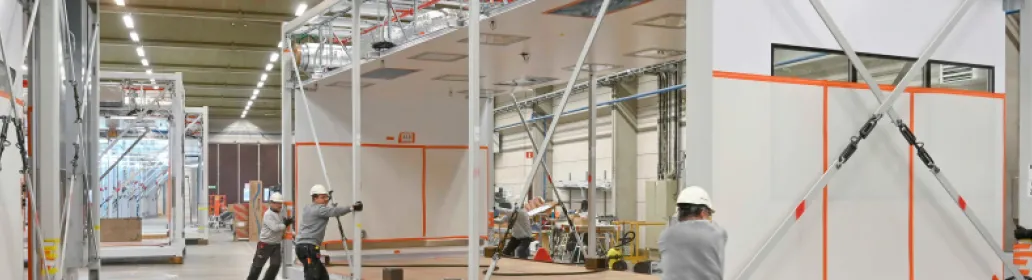